What Is Phosphating?
Phosphate coating can be defined as the process in which the phosphate coating solution forms an insoluble phosphate layer on a metal surface by dipping, spraying or any other method. For the formation of this type of coating the content of the prepared solution must contain hydrogen ion (H+), phosphate anion (PO4-3) and at least one metal cation in order to obtain surface pickling on the metal and proper pH.
Phosphating of metals is one of the most important of surface treatment methods and a number of modern metal finishing procedures would not be possible without it.
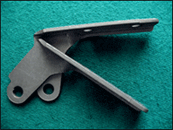
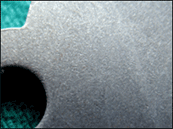
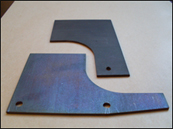
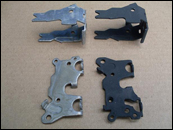
The Main Areas Of Application Of Phosphating
- Corrosion protection in conjunction with organic coatings, e.g., paints and polymer films,
- Facilitation of cold-forming processes, e.g., wire drawing and tube drawing, deep drawing,
- Corrosion protection in conjunction with oils and waxes,
- Corrosion protection with no subsequent treatment.
Phosphate Coating Processes
Phosphating can be executed using a variety of sequential processes. The list of these and whether they are in fact called for or not, depends on many factors of which the most important are; nature of the metal to be coated, shape and surface condition of the metal, number of parts and uniformity of their surface state, anticipated service duty of the phosphate coating, Organisational factors, e.g., limit on number of processing lines.
The phosphating sequence is normally broken down into the following stages:
- Degreasing and cleaning
- Derusting and descaling
- Activation
- Phosphating
- Post-treatment
There is normally a rinse between the individual processing steps in order to remove the solution layer from the metal surface and to avoid carry-over of this as an impurity to the subsequent stage. According to circumstances, the processing sequence may be longer or shorter. Thus, for example, pickling can be omitted if no corrosion products are present on the metal surface. Then, too, some of the individual stages can be combined, for example, cleaning and phosphating.
Phosphate Coating Types
Of the many phosphating systems which have been proposed, the following are of industrial importance: Zinc phosphate, iron phosphate, manganese phosphate. Such phosphating systems are predominantly applied to iron and steel, as well as zinc surfaces whereas other metals which can be phosphated, e.g., aluminium, magnesium are less commonly processed by this method.
Surface Preparation Before Phosphate Coating
Phosphate coatings which adhere well to the basis metal and which, so far as possible, cover it completely, can only be formed on clean surfaces which are free from rust, scale, soot and other corrosion products. Oil and grease films likewise inhibit phosphate coating formation, except when they are so thin that they are removed by initial etching stage.
The nature of the pretreatment steps used before the phosphating itself, e.g., in the cleaning, can considerably affect the growth rate of the phosphate coating, its thickness and the crystal size. These effects can be chemical or mechanical and sometimes both together.
The effect of metal pretreatment on coating weight depends on the phosphating temperature. At high bath temperatures, the phosphate crystals form on the blasted steel are largely of uniform size and very fine. On samples which have only been degreased, very large and very small crystals co-exists, whereas on blasted steel, there is much more uniform coverage of very small crystals.
Chemical pretreatment of the metal, too, can significantly affect the formation of the phosphate coating. These observations have industrial significance in terms of alkaline degreasing and solvent degreasing as well as acid pickling. Phosphating solutions based on zinc, iron and manganese produce rougher phosphate coatings with higher weight per unit area, when strong alkaline cleaners are used, in contrast to solvent degreasing. In addition, longer phosphating times are required for complete coverage of the metal.
To suggest that a large range of steels are capable of being phosphated is not to imply that, in all cases, these are suitable for industrial applications. Thus it has been found that deep-drawn steel, as widely used in automobile industry, can be phosphated, painted and subjected to accelerated corrosion testing.
All zinc-containing materials industrially used, including electrogalvanized and hot-dip galvanized steels, as well as zinc with small additions of copper or titanium, used, for example, in diecastings, can be phosphated without problems. To improve corrosion resistance and "white rust" formation, chromate passivation films must first be removed.
Phosphate Coating Color And Image
The colour of the phosphate coatings lies between light gray and pitch black. The lightest are the zinc phosphate coatings on zinc which, when this is the only metal in the bath, contain no other cationic species. When iron (II) also is present, and especially zinc and nickel, darker, usually, mid-grey coatings are formed. Whit steel substrates zinc phosphate coatings are darker than on zinc substrates, which is explained in terms of the larger amount of iron in the coating. Zinc-calcium baths produce coatings of similar hues to the zinc-only baths. Very dark, anthracite-black coatings result from the phosphating of steel in manganese-based solutions.